Product Design
Product Design
Product Design
When we're contacted about a product to be designed, we start by doing intensive work with the client to develop a formal specification for the product. This is followed by iterations of sketches, mockups, and early or partial prototypes. We fabricate in-house and also work with our network of vendors for materials, components, and services, and then provide delivery of final prototypes and a full design package. Our design process includes Solidworks Pro, CAMworks for CNC milling, Solidworks Visualize for rendering of photorealistic images, Photoshop, and Blender. In many circumstances, we can also handle limited amounts of early and short-run manufacturing.
When we're contacted about a product to be designed, we start by doing intensive work with the client to develop a formal specification for the product. This is followed by iterations of sketches, mockups, and early or partial prototypes. We fabricate in-house and also work with our network of vendors for materials, components, and services, and then provide delivery of final prototypes and a full design package. Our design process includes Solidworks Pro, CAMworks for CNC milling, Solidworks Visualize for rendering of photorealistic images, Photoshop, and Blender. In many circumstances, we can also handle limited amounts of early and short-run manufacturing.
When we're contacted about a product to be designed, we start by doing intensive work with the client to develop a formal specification for the product. This is followed by iterations of sketches, mockups, and early or partial prototypes. We fabricate in-house and also work with our network of vendors for materials, components, and services, and then provide delivery of final prototypes and a full design package. Our design process includes Solidworks Pro, CAMworks for CNC milling, Solidworks Visualize for rendering of photorealistic images, Photoshop, and Blender. In many circumstances, we can also handle limited amounts of early and short-run manufacturing.
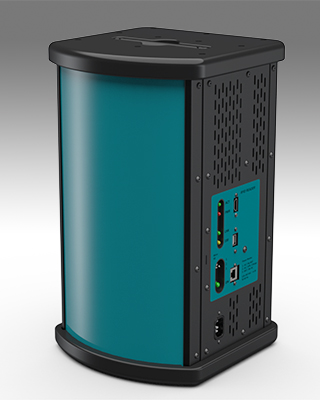
Portable RFID Reader
This project included a high level of system integration, power management, and specification of electronic components. The design and fabrication tasks included sheet metal enclosure parts, machined plastic end caps and other plastic parts, a compartment for an optional removable battery pack, several labels, accessory antenna mounts, an aluminum tripod stand mount, a retractable aluminum carrying handle, and spray finishing the front panel, . After assembly, we also performed initial electrical testing on each unit.
A couple of short production runs were made for this reader.
Portable RFID Reader
This project included a high level of system integration, power management, and specification of electronic components. The design and fabrication tasks included sheet metal enclosure parts, machined plastic end caps and other plastic parts, a compartment for an optional removable battery pack, several labels, accessory antenna mounts, an aluminum tripod stand mount, a retractable aluminum carrying handle, and spray finishing the front panel, . After assembly, we also performed initial electrical testing on each unit.
A couple of short production runs were made for this reader.
Portable RFID Reader
This project included a high level of system integration, power management, and specification of electronic components. The design and fabrication tasks included sheet metal enclosure parts, machined plastic end caps and other plastic parts, a compartment for an optional removable battery pack, several labels, accessory antenna mounts, an aluminum tripod stand mount, a retractable aluminum carrying handle, and spray finishing the front panel, . After assembly, we also performed initial electrical testing on each unit.
A couple of short production runs were made for this reader.
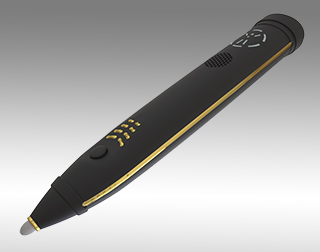
Handheld Device for Use in the Health & Wellness Industry
This was one of a series of proof-of-concept prototypes created as part of a design project for a startup company. This prototype was designed to fit a large number of potential electronic and mechanical features into one evaluation package. Numerous stakeholders had requirements that had to be included in the design, particularly from the electronic design team.
See more information about this project at Biotech & Medical and Rapid Prototyping.
Handheld Device for Use in the Health & Wellness Industry
This was one of a series of proof-of-concept prototypes created as part of a design project for a startup company. This prototype was designed to fit a large number of potential electronic and mechanical features into one evaluation package. Numerous stakeholders had requirements that had to be included in the design, particularly from the electronic design team.
See more information about this project at Biotech & Medical and Rapid Prototyping.
Handheld Device for Use in the Health & Wellness Industry
This was one of a series of proof-of-concept prototypes created as part of a design project for a startup company. This prototype was designed to fit a large number of potential electronic and mechanical features into one evaluation package. Numerous stakeholders had requirements that had to be included in the design, particularly from the electronic design team.
See more information about this project at Biotech & Medical and Rapid Prototyping.
Ford DeWalt Tool Link RFID System
Ford DeWalt Tool Link RFID System
Ford DeWalt Tool Link RFID System
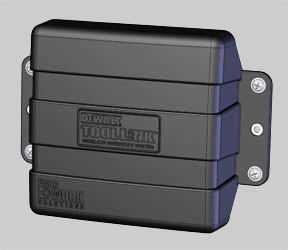
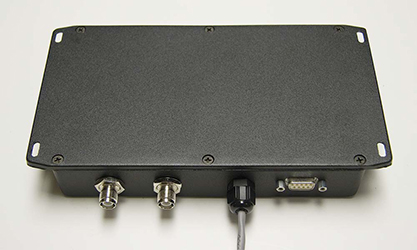
This system was an option for some Ford pickup trucks and other vehicles, allowing remote tracking of tagged tools from the truck cab to the truck bed or other storage section. We provided comprehensive mechanical design and support for this project, delivering multiple iterations of designs and prototypes on a tight schedule and coordinating with a large team of design, planning and manufacturing personnel as well as engineers and project managers inside Ford and their affiliates in the auto industry.
See the Wired article about Tool Link.
Our design work included the injection-molded antenna shroud, (see image) several steel support brackets, a machined heatsink, two molded rubber seals, and die-cut thermal pads. We also modified an existing die-cast environmentally sealed enclosure (see image) to hold the RFID circuitry and a group of sealed connectors, and specified all of the mounting hardware. All parts were designed to meet Ford's durability specs and to be ROHS compliant. All electronic packaging had to be environmentally sealed, and numerous components and assemblies had to pass Ford's shock, vibration, environmental, and impact tests across a wide temperature range. All tested components and assemblies passed on their first try.
This system was an option for some Ford pickup trucks and other vehicles, allowing remote tracking of tagged tools from the truck cab to the truck bed or other storage section. We provided comprehensive mechanical design and support for this project, delivering multiple iterations of designs and prototypes on a tight schedule and coordinating with a large team of design, planning and manufacturing personnel as well as engineers and project managers inside Ford and their affiliates in the auto industry.
See the Wired article about Tool Link.
Our design work included the injection-molded antenna shroud, (see image) several steel support brackets, a machined heatsink, two molded rubber seals, and die-cut thermal pads. We also modified an existing die-cast environmentally sealed enclosure (see image) to hold the RFID circuitry and a group of sealed connectors, and specified all of the mounting hardware. All parts were designed to meet Ford's durability specs and to be ROHS compliant. All electronic packaging had to be environmentally sealed, and numerous components and assemblies had to pass Ford's shock, vibration, environmental, and impact tests across a wide temperature range. All tested components and assemblies passed on their first try.
This system was an option for some Ford pickup trucks and other vehicles, allowing remote tracking of tagged tools from the truck cab to the truck bed or other storage section. We provided comprehensive mechanical design and support for this project, delivering multiple iterations of designs and prototypes on a tight schedule and coordinating with a large team of design, planning and manufacturing personnel as well as engineers and project managers inside Ford and their affiliates in the auto industry.
See the Wired article about Tool Link.
Our design work included the injection-molded antenna shroud, (see image) several steel support brackets, a machined heatsink, two molded rubber seals, and die-cut thermal pads. We also modified an existing die-cast environmentally sealed enclosure (see image) to hold the RFID circuitry and a group of sealed connectors, and specified all of the mounting hardware. All parts were designed to meet Ford's durability specs and to be ROHS compliant. All electronic packaging had to be environmentally sealed, and numerous components and assemblies had to pass Ford's shock, vibration, environmental, and impact tests across a wide temperature range. All tested components and assemblies passed on their first try.
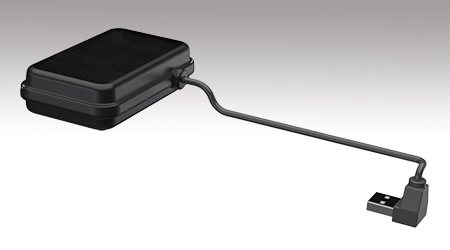
Rugged Environmentally Sealed Enclosure
This enclosure holds a wireless device. Prototype enclosure halves were CNC milled from polycarbonate. The enclosure is sealed to IP67, has a pressure vent, and was subjected to multiple drops per MIL-STD-810G before immersion testing. In production, the two halves of the enclosure were injection molded from polycarbonate.
Rugged Environmentally Sealed Enclosure
This enclosure holds a wireless device. Prototype enclosure halves were CNC milled from polycarbonate. The enclosure is sealed to IP67, has a pressure vent, and was subjected to multiple drops per MIL-STD-810G before immersion testing. In production, the two halves of the enclosure were injection molded from polycarbonate.
Rugged Environmentally Sealed Enclosure
This enclosure holds a wireless device. Prototype enclosure halves were CNC milled from polycarbonate. The enclosure is sealed to IP67, has a pressure vent, and was subjected to multiple drops per MIL-STD-810G before immersion testing. In production, the two halves of the enclosure were injection molded from polycarbonate.
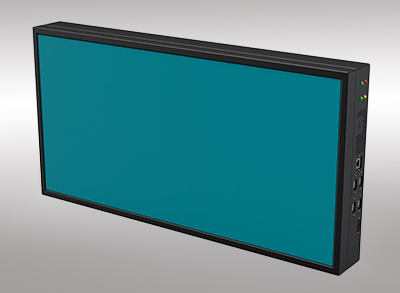
RFID Reader for Wall or Ceiling Mounting
This project included electronic system integration and power management. The design and fabrication tasks included sheet metal enclosure parts, a VESA bracket adapter, and sprayfinishing the front panel. After assembly, we also performed initial electrical testing on each unit.
A couple of short production runs were made for this reader.
RFID Reader for Wall or Ceiling Mounting
This project included electronic system integration and power management. The design and fabrication tasks included sheet metal enclosure parts, a VESA bracket adapter, and sprayfinishing the front panel. After assembly, we also performed initial electrical testing on each unit.
A couple of short production runs were made for this reader.
RFID Reader for Wall or Ceiling Mounting
This project included electronic system integration and power management. The design and fabrication tasks included sheet metal enclosure parts, a VESA bracket adapter, and sprayfinishing the front panel. After assembly, we also performed initial electrical testing on each unit.
A couple of short production runs were made for this reader.
design@design-innovation.org 781-883-5666
design@design-innovation.org 781-883-5666
design@design-innovation.org
781-883-5666